TPMS-infill MMC-based topology optimization considering overlapped
component property
Engineering designs involving multiple materials suffer either difficult interface modeling or finding physically
meaningful transition domains with a clear or even optimal structural representation. However, previous material interpolation models often cannot achieve either of them. A new function interpolation scheme is proposed
in this work by leveraging the triply periodic minimal surfaces (TPMS). This TMPS-based architecture will serve
as the infill morphology at the microstructural scale, while its distribution at the higher structural scale will be
achieved by topology optimization (TO). The moving morphable component (MMC)-based TO is adopted to first
reduce the number of design variables and then provide explicit structural geometries. For finite elements where
multiple materials exist (or the overlapping component area), level set functions are constructed to identify the
interpolation parameters to determine the TMPS with clear material characteristics. This framework will thus
allow us to generate new architected materials associated with the optimized design variable at the structural
scale, while guaranteeing a smooth and meaningful transition at lower material microstructures. Numerical
examples show that stress concentration can be significantly reduced because of the distinguished compatibility
inside the heterogeneous structure, which leads to its successful manufacturing by the 3D printing. Finally, a real
engineering case for the design of an automotive connecting rod is presented to illustrate the versatility of the
proposed approach.
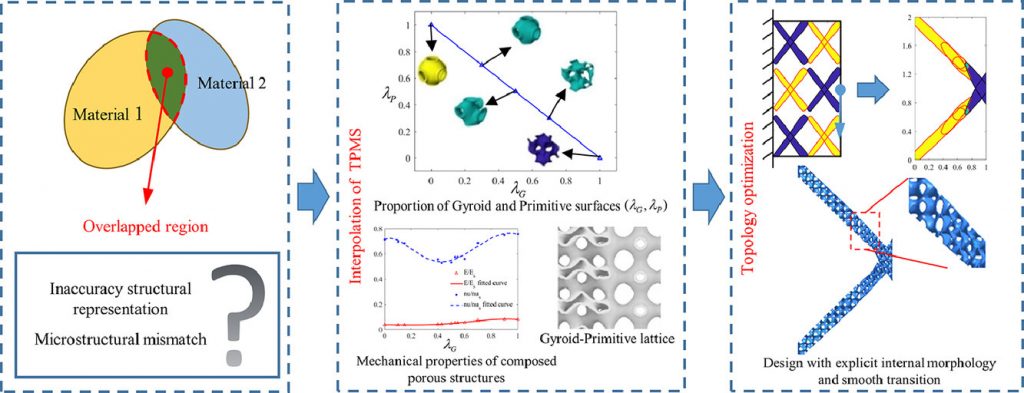